In the ever-evolving landscape of business, process improvement and mapping tools play a crucial role in enhancing efficiency. They identify challenges and ensure an optimal performance. These tools serve as guides, helping organizations streamline operations, enhance productivity, and achieve strategic objectives. These tools stand out as powerful frameworks for visualizing processes and driving continuous improvement.
Today, we'll delve into one of the most essential tools for process improvement and mapping: the SIPOC model. We'll cover this comprehensive framework in detail. We’ll explore its applications, step-by-step approach, examples, advantages, disadvantages, and frequently asked questions. Get ready to gain valuable insights into how the SIPOC model can streamline your existing processes.
What is the SIPOC Model?
The SIPOC analysis is an acronym standing for Suppliers, Inputs, Processes, Outputs, and Customers. It is a structured tool used in process improvement and mapping.
It provides a clear framework for identifying and understanding the essential elements of a process. This includes its stakeholders, inputs, activities, and outcomes. Organizations can gain valuable insights into process dynamics and opportunities for enhancement.
The SIPOC model serves as a foundational tool in various industries, including manufacturing, healthcare, and service sectors. Its simplicity and effectiveness make it accessible to team members and individuals at all levels of an organization. The companies can visualize the end-to-end process flow and the stakeholders involved. They can streamline operations, enhance quality, and drive sustainable performance improvements.
The SIPOC Model: Explained
The SIPOC model is a valuable tool for process mapping and improvement. The acronym stands for Suppliers, Inputs, Processes, Outputs, and Customers. It provides a high-level overview of a process by identifying key elements and their relationships. Suppliers are entities that provide inputs to the process, ranging from raw materials to information or services.
Understanding supplier capabilities and dependencies is crucial for ensuring process reliability and quality. Inputs represent the resources or information required to initiate and execute the process. These can include materials, data, instructions, or requirements. Identifying and managing inputs effectively is essential for achieving desired process outcomes.
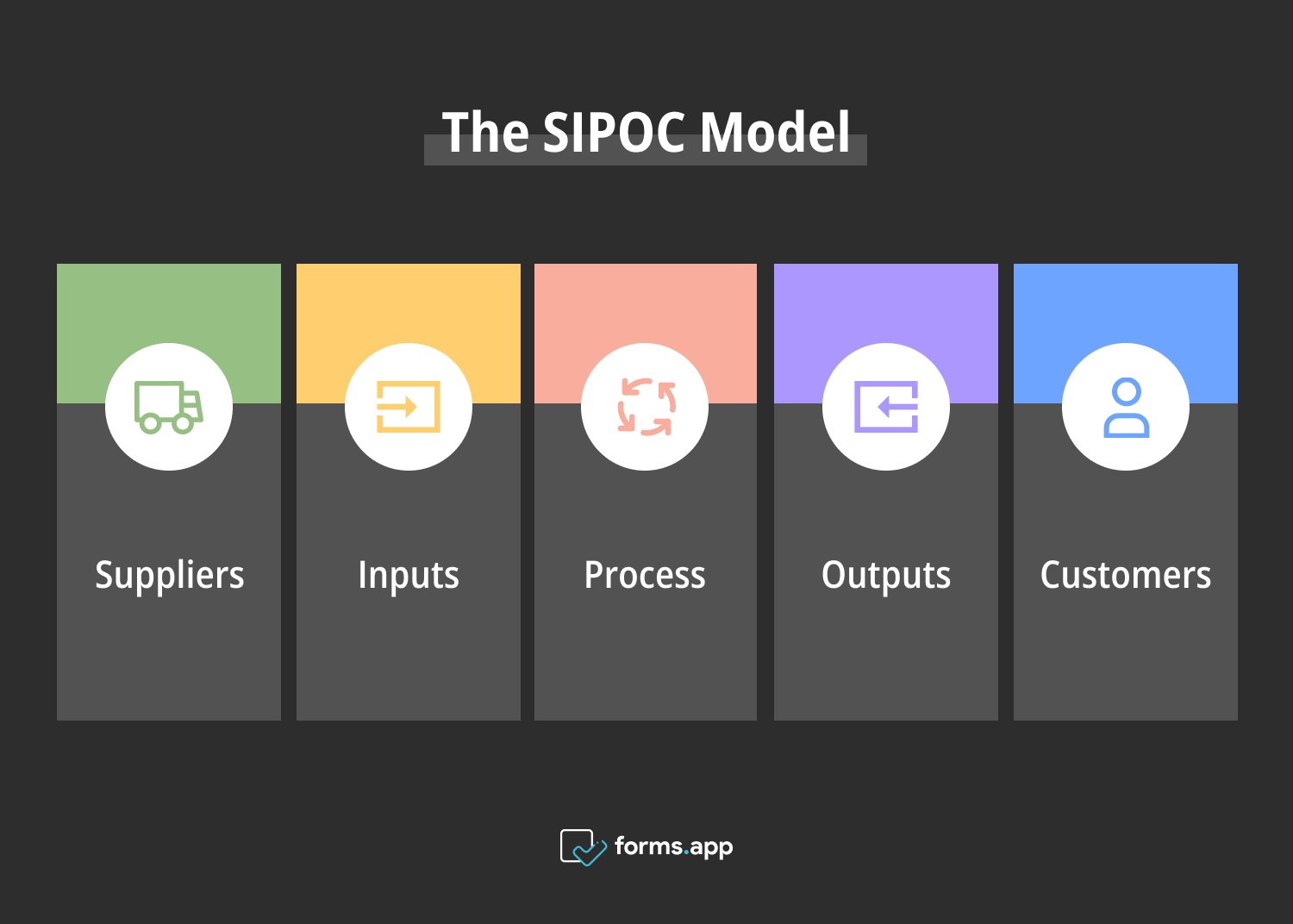
The SIPOC Model diagram
1- Suppliers
Suppliers represent entities providing necessary resources or materials. They can be internal or external for the organization. Internally, suppliers might include departments or teams. Externally, they include vendors or service providers.
Understanding supplier capabilities and quality is vital for ensuring smooth processes.
Evaluating supplier performance helps in managing risks and optimizing resource allocation. Effective communication and collaboration with suppliers foster better relationships and enhance process efficiency. Companies can identify the suppliers and analyze them. They can mitigate dependency risks and ensure a consistent flow of inputs.
2- Inputs
Inputs are the raw materials, information, or resources required to initiate and sustain a process. They serve as the building blocks for generating outputs. Inputs can vary from tangible materials to intangible data or knowledge.
Understanding the quality, quantity, and timeliness of inputs is crucial for process effectiveness.
Assessing input specifications ensures alignment with desired output standards. Inputs might include physical materials, software systems, human resources, or financial resources. Proper handling and management of inputs contribute to overall process efficiency and product quality. Analyzing input sources and characteristics enables organizations to streamline operations and minimize wastage.
3- Process
The Process component of the SIPOC model outlines the series of activities or steps involved. These transform the inputs into outputs. It delineates the workflow, procedures, and interactions within the process. Understanding process intricacies helps in identifying bottlenecks, redundancies, and opportunities for improvement.
Mapping the process flow facilitates clarity and transparency.
This aids in effective management and troubleshooting. Analyzing process performance metrics enables organizations to measure efficiency, quality, and adherence to standards. Continuous process monitoring and optimization are essential for enhancing productivity and reducing costs. Aligning process objectives with organizational goals ensures strategic coherence and competitiveness.
4- Outputs
Outputs represent the products, services, or outcomes generated by the process. They fulfill the intended purpose and meet the requirements of customers or stakeholders. Outputs can be tangible goods, digital content, reports, or services rendered.
Assessing output quality, quantity, and timeliness is crucial for meeting customer expectations and organizational objectives.
Monitoring output specifications ensures compliance with standards and regulations. Delivering excellent outputs enhances customer satisfaction and loyalty. Analyzing output feedback enables organizations to identify areas for enhancement and innovation. Effective output management is vital for maintaining competitiveness and market relevance.
5- Customers
Customers are the recipients of the outputs produced by the process. They can be internal or external to the organization. Internal customers may include downstream processes or departments relying on outputs for further operations. External customers encompass end-users, clients, or stakeholders receiving products or services.
Understanding customer needs, preferences, and feedback is essential for delivering value and ensuring satisfaction.
Building strong customer relationships fosters loyalty and promotes repeat business. Adapting to changing customer demands drives innovation and market relevance. By focusing on customer-centricity, organizations can sustainably grow and thrive in competitive environments.
Example of the SIPOC Model
There are many SIPOC examples in today’s business life. Here, let’s look at an example scenario. We have Company X, which is a leading manufacturer of automotive components using the SIPOC model. Witness the positive results the Company X obtains:
1- Suppliers
Company X, a leading manufacturer of automotive components, implemented the SIPOC model to streamline its supply chain. The company identifies key suppliers of raw materials and components, such as steel, rubber, and electronics. It ensures a stable flow of inputs. Through rigorous supplier evaluations and collaborations, they improved delivery times and negotiated better pricing, reducing production costs and mitigating supply chain risks.
2- Inputs
With the SIPOC model, Company X assessed input specifications and quality standards. They optimized their procurement processes to ensure the timely delivery of high-quality materials. By investing in advanced inventory management systems, they maintained optimal stock levels, reducing production delays and minimizing wastage. This led to improved product quality and enhanced manufacturing efficiency.
3- Process
Company X mapped out their manufacturing processes using the SIPOC model, identifying areas for improvement and optimization. They streamlined production workflows, implemented lean manufacturing principles, and invested in automation technologies. By standardizing procedures and enhancing workflow transparency, they reduced lead times and improved production throughput. Continuous process monitoring and refinement enabled Company X to meet customer demand fluctuations effectively.
4- Outputs
Through the SIPOC model, Company X focused on delivering superior outputs to its customers. They prioritized product quality, reliability, and performance, aligning output specifications with customer requirements. By leveraging feedback mechanisms and conducting regular quality audits, they ensured consistent output excellence. This resulted in increased customer satisfaction, loyalty, and a positive brand reputation, driving repeat business and market expansion.
5- Customers
Company X placed a strong emphasis on understanding customer needs and preferences. Through market research and customer feedback analysis, they identified emerging trends and evolving customer demands. By tailoring their product offerings and providing responsive customer support, Company X strengthened customer relationships and market competitiveness.
Outcome
This customer-centric approach enhanced brand loyalty. It enabled Company X to secure long-term partnerships and penetrate new market segments. Ultimately, by utilizing the SIPOC model, Company X achieved sustained growth and profitability in the competitive manufacturing industry.
How to use the SIPOC Model
Implementing the SIPOC model effectively requires careful planning and execution. By following a structured approach, organizations can gain valuable insights into their processes and drive continuous improvement. There are eight key steps involved in a proper implementation of the SIPOC model. These ensure comprehensive analysis and optimization of business operations.
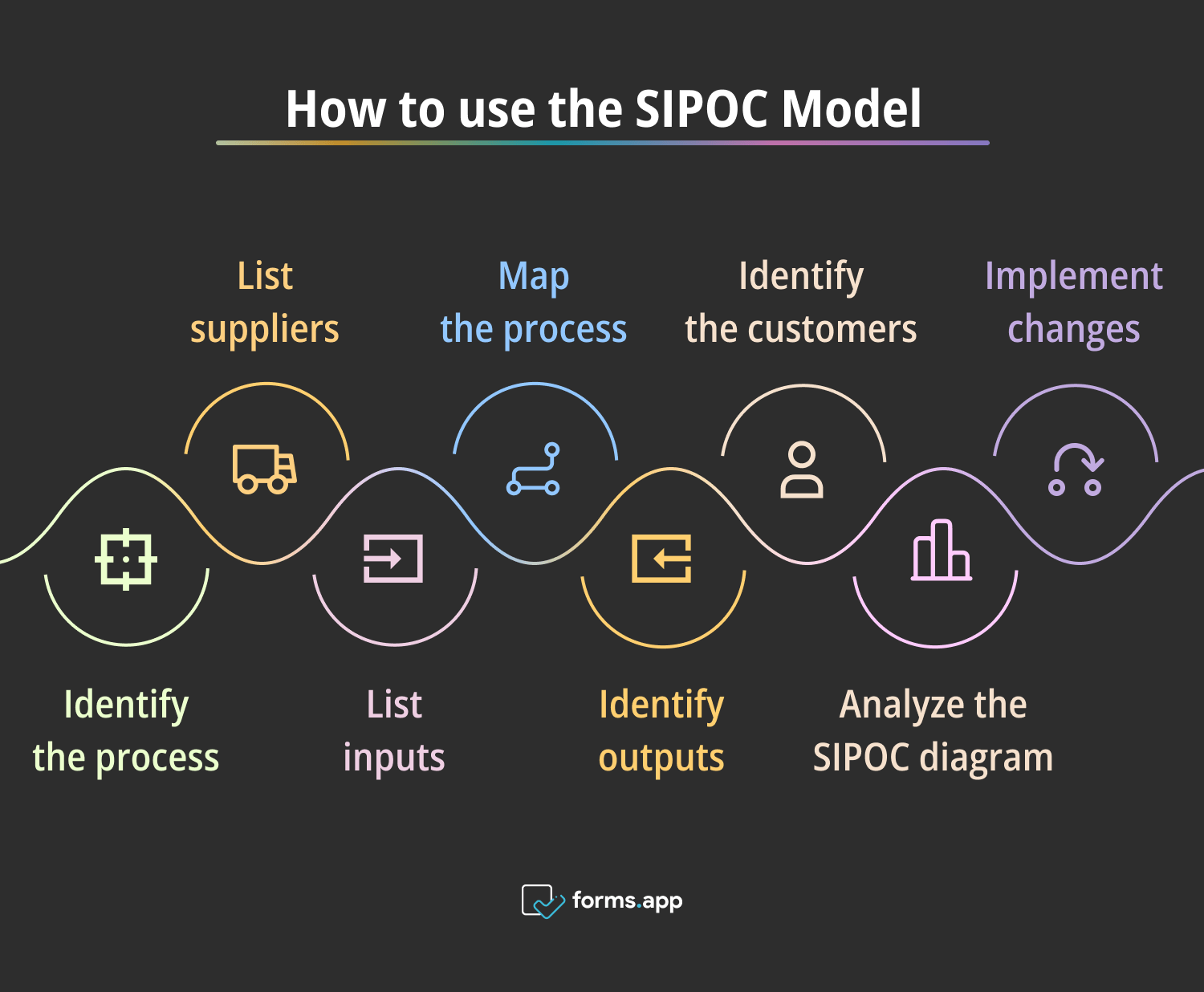
The SIPOC Model steps
- Identify the process: Determine the specific process that you want to analyze or improve using the SIPOC model. This could be a core business operation or a particular project management.
- List suppliers: Identify all the entities that provide inputs or resources to the process. These could include internal departments, external vendors, or relevant stakeholders contributing to the process.
- List inputs: Identify all the inputs required to initiate and sustain the process. This includes raw materials, information, resources, or any other factors necessary for the process to function.
- Map the process: Outline the steps involved in the process from start to finish. This involves documenting the sequence of activities, decision points, and interactions between different stages of the process.
- Identify outputs: Determine the desired outputs or outcomes generated by the process. These could be products, services, reports, or any other deliverables that result from completing the process.
- Identify the customers: Identify the individuals, groups, or entities who receive or benefit from the outputs of the process. This could include internal stakeholders, external customers, or other parties impacted by the process outcomes.
- Analyze the SIPOC diagram: Review the completed SIPOC diagram to identify potential areas for improvement or optimization within the process. Look for bottlenecks, redundancies, or opportunities to enhance efficiency and effectiveness.
- Implement changes: Based on the analysis, implement changes or initiatives aimed at improving business processes. This could involve streamlining workflows, optimizing resource allocation, or enhancing communication and collaboration between stakeholders. Monitor the effects of these changes and iterate as necessary to achieve desired outcomes.
When to use the SIPOC Model
The SIPOC model is invaluable in numerous organizational contexts. It is particularly beneficial when there is a need to gain a comprehensive understanding of a process. It is also helpful to identify stakeholders, and clarify roles and responsibilities. From process improvement initiatives to project planning and supply chain optimization, the SIPOC model serves as a versatile framework for achieving organizational objectives efficiently.
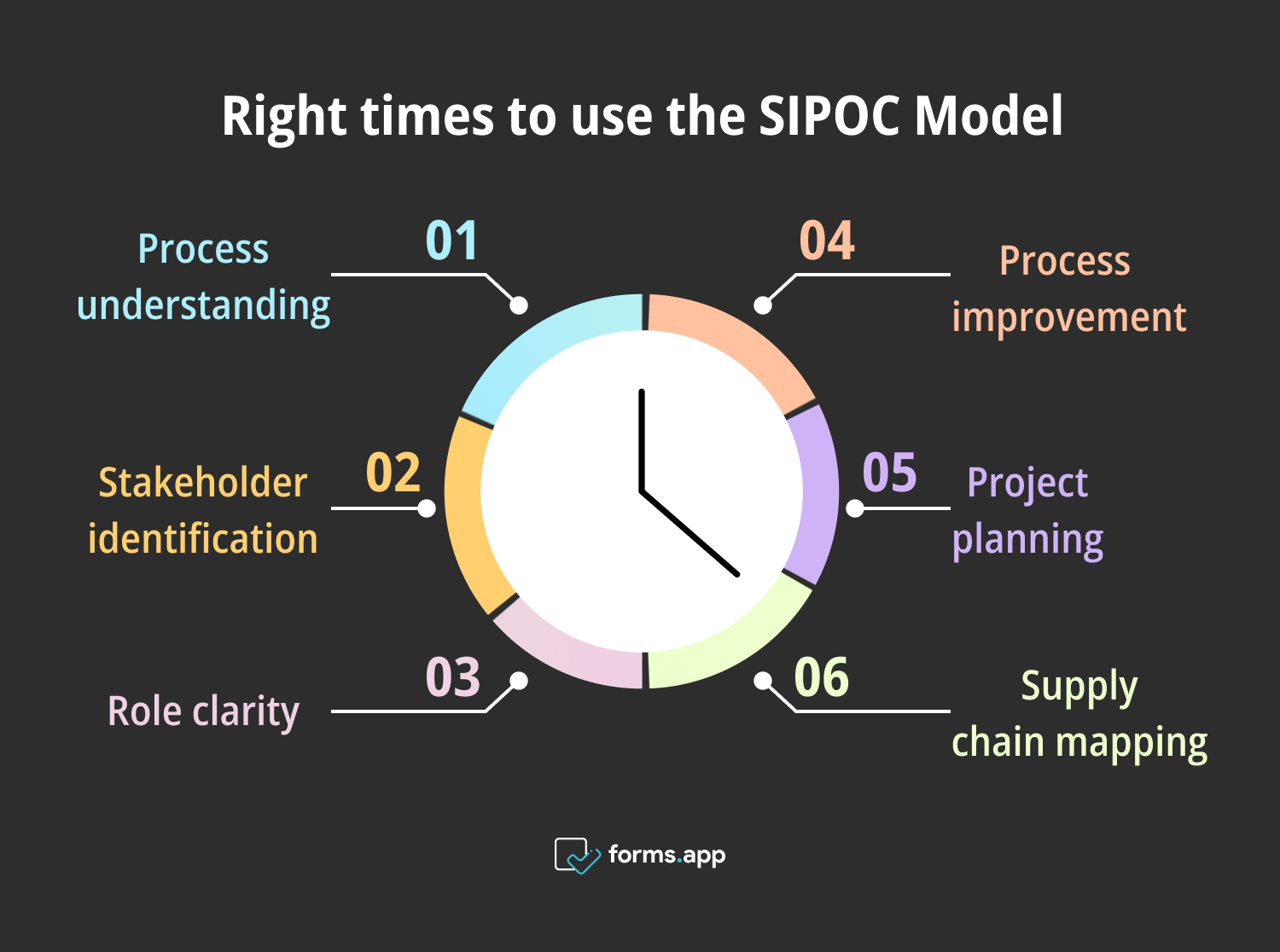
Correct times to use the SIPOC Model
⏰Process understanding: The SIPOC model offers clarity on complex processes. It helps stakeholders grasp the sequence of activities, inputs, and outputs involved. It aids in identifying essential process elements and understanding their connections for better decision-making and optimization.
⏰Stakeholder identification: By outlining Suppliers, Inputs, Processes, Outputs, and Customers, the SIPOC model facilitates the identification of stakeholders involved in a process. This ensures comprehensive engagement, effective communication, and alignment of objectives across the organization.
⏰Role clarity: Utilizing the SIPOC model clarifies roles and responsibilities within a process, ensuring that each stakeholder understands their contributions and dependencies. This fosters accountability, reduces ambiguity, and enhances collaboration, ultimately improving overall process efficiency and effectiveness.
⏰Process improvement: The SIPOC model serves as a valuable tool for process improvement initiatives. It provides a structured framework for analyzing process elements and identifying areas for enhancement. It enables organizations to streamline workflows, eliminate bottlenecks, and optimize resource allocation to achieve desired outcomes efficiently.
⏰Project planning: Including the SIPOC model in project planning allows teams to map out project scope. It also helps identify necessary resources and align activities with project objectives. It provides a clear overview of project requirements, helping to mitigate risks. It ensures project success, and delivering value to stakeholders.
⏰Supply chain mapping: The SIPOC model aids in mapping out supply chains. It identifies key suppliers, inputs, processes, outputs, and customers involved in the flow of goods or services. This enables organizations to optimize supply chain operations, manage risks, and enhance overall supply chain performance effectively.
Pros and Cons of the SIPOC Model
The SIPOC model presents both advantages and limitations. Creating a SIPOC diagram offers clarity, stakeholder engagement, efficiency improvement, scope definition, enhanced communication, and continuous improvement opportunities. However, potential drawbacks include simplification, limited detail for complex processes, and challenges due to its static nature.
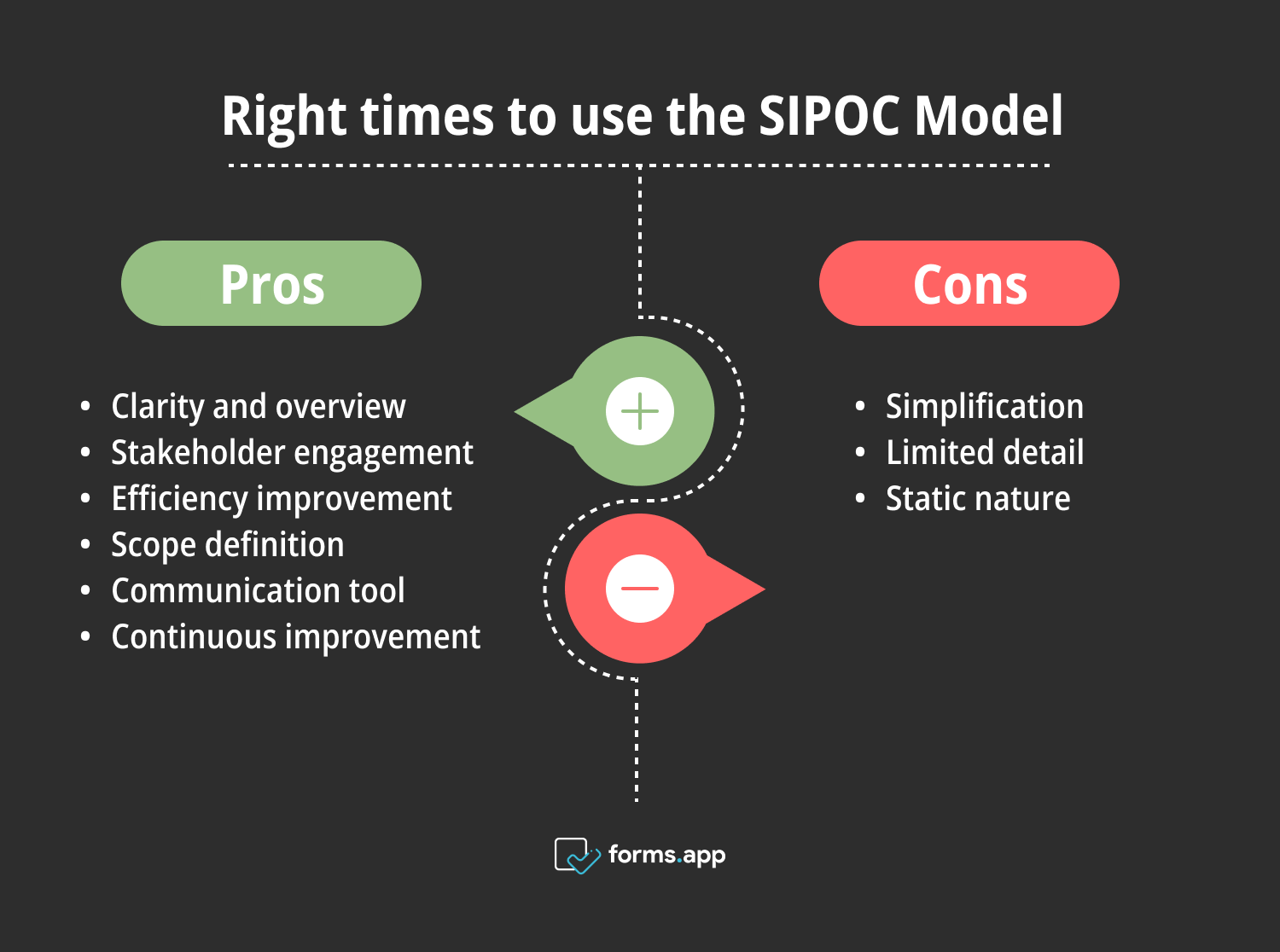
Advantages and Disadvantages of the SIPOC Model
1- Pros of the SIPOC Model
- Clarity and overview: The SIPOC model provides a clear and concise overview of a process. It ensures stakeholders understand its components and objectives, fostering alignment and informed decision-making.
- Stakeholder engagement: By identifying key stakeholders and their roles, the SIPOC model promotes collaboration, communication, and accountability throughout the process lifecycle.
- Efficiency improvement: Through visualizing process steps and dependencies, the SIPOC model enables teams to identify bottlenecks, redundancies, and opportunities for optimization. It leads to enhanced efficiency and productivity.
- Scope definition: It assists in clearly defining the scope and boundaries of projects or processes. It ensures teams have a shared understanding of objectives and deliverables.
- Communication tool: The SIPOC model serves as a visual tool. It brings effective communication among cross-functional teams, enabling clearer discussions, problem-solving, and decision-making.
- Continuous improvement: Utilizing the SIPOC model encourages a culture of continuous improvement. It does so by providing a structured framework for identifying and addressing process inefficiencies specifically. It drives ongoing enhancements and innovation.
2- Cons of the SIPOC Model
- Simplification: The SIPOC model may simplify complex processes. It potentially overlooks critical details or nuances essential for thorough analysis and improvement, leading to incomplete solutions or missed opportunities.
- Limited detail: Its high-level nature may lack the depth needed for comprehensive analysis, for highly specialized processes. It may hinder the ability to identify root causes or implement targeted solutions effectively.
- Static nature: The SIPOC model's static structure may not easily accommodate changes or evolving process requirements. It may require frequent updates to remain relevant. This can be time-consuming and resource-intensive.
Frequently asked questions about the SIPOC Model
The following frequently asked questions address common inquiries about the SIPOC model, a structured tool used for process mapping and improvement. Learn about its definition, origin, benefits, and objectives to gain a comprehensive understanding of its utility within organizational contexts.
The SIPOC model, an acronym for Suppliers, Inputs, Process, Outputs, and Customers, is a structured tool used to map out and understand processes. It provides a high level steps of a process. It outlines the key components, stakeholders, and interactions to aid in analysis, improvement, and communication within organizations.
The exact origin of the SIPOC model is unclear. But it leans on the Six Sigma methodology as a tool for process mapping and improvement. Its development likely evolved through collaborative efforts within the quality management and process improvement communities over time.
The primary benefit of the SIPOC model lies in its ability to provide clarity, alignment, and insight into processes. One can visualize key components such as suppliers, inputs, processes, outputs, and customers. It helps organizations understand process flows, identify stakeholders, clarify roles, and drive improvement initiatives effectively.
The objective of the SIPOC model is to facilitate a structured approach to process mapping and improvement. It aims to provide a clear and concise overview of a process and identify its critical elements and interactions. It also clarifies roles and responsibilities and aligns stakeholders to drive efficiency, effectiveness, and continuous improvement within organizations.
Conclusion
To sum up, the SIPOC model is a versatile tool for process mapping and improvement. It provides a structured approach to understanding processes by outlining key components. It aids in clarifying roles, engaging stakeholders, and driving continuous improvement initiatives, ultimately enhancing organizational efficiency, effectiveness, and alignment.
In this article, we have covered the SIPOC model with all of its aspects, its steps, advantages and disadvantages and suitable environments. We have also examined the frequently asked questions about the subject. Now that you have learned about this practical tool create your own SIPOC model template and elevate your business!
Fatih is a content writer at forms.app and a translator specializing in many text domains, including medical, legal, and technical. He loves studying foreign languages. Fatih especially likes to create content about program management, organizational models, and planning tools.